End-Products of a Pyrolysis Plant and Their Industrial Applications
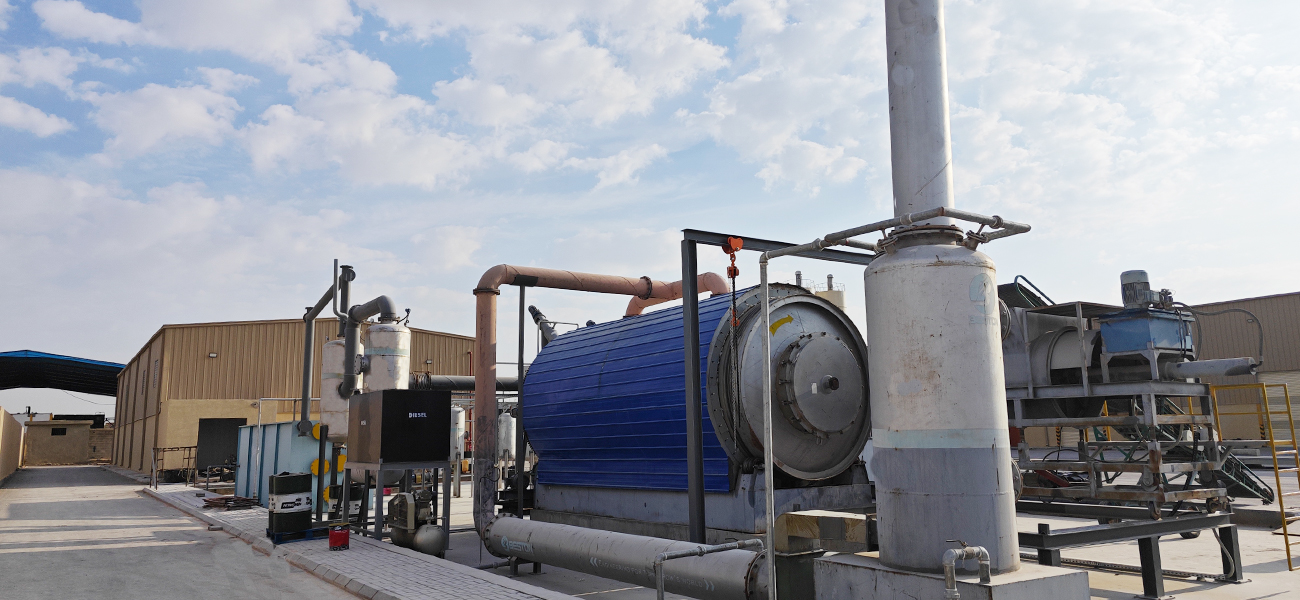
A pyrolysis unit offers a transformative solution for the treatment of organic solid waste, especially end-of-life tires. Through thermochemical decomposition in an oxygen-deficient environment, materials are converted into multiple value-added products. These outputs play critical roles in various industrial sectors, contributing to resource efficiency, waste minimization, and energy diversification. Whether operating a batch-style tire to oil plant or a fully automated continuous waste tyre pyrolysis plant, the final product composition remains largely consistent, albeit with variation in yield and purity.
Pyrolysis Oil
The most economically significant product from a tire pyrolysis plant is pyrolysis oil. This dark, viscous liquid is a complex mixture of aliphatic and aromatic hydrocarbons with high calorific value, typically ranging from 40 to 45 MJ/kg. After distillation, the oil can be upgraded to various commercial fuel grades.
Industrial Applications:
Carbon Black
The solid residue derived from pyrolysis, commonly referred to as recovered carbon black (rCB), accounts for 30–35% of the total output. It consists mainly of unburned carbon, mineral ash, and trace elements. In a continuous waste tyre pyrolysis plant, optimized thermal control enhances the carbon purity and fineness, improving its marketability.
Industrial Applications:
Combustible Gas
A byproduct of the thermal cracking process, the syngas produced in a tire to oil plant contains hydrogen, methane, and light hydrocarbons. Rather than being released, modern systems capture and combust this gas to supply internal heat, significantly reducing external fuel dependency.
Industrial Applications:
Steel Wire
Tire casings contain a substantial amount of high-tensile steel, especially in radial designs. Upon pyrolysis, this steel is liberated and extracted via magnetic separation systems integrated into the pyrolysis unit.
Industrial Applications:
Conclusion
The end-products of a tire pyrolysis plant embody the principle of industrial symbiosis. Each output—whether liquid, solid, or gaseous—serves as a feedstock for diverse sectors ranging from energy to manufacturing. As demand intensifies for circular economy solutions, the tire to oil plant and its derivatives stand at the forefront of sustainable resource utilization. The integration of these systems, especially in the form of a continuous waste tyre pyrolysis plant, offers scalable, high-efficiency processing with tangible environmental and economic returns.