Everything You Need To Know About A Continuous Pyrolysis Plant
The term “pyrolysis” is used to refer to the simultaneous chemical and physical reactions in organic substances when they are exposed to very high temperatures. Generally speaking, a continuous waste tire pyrolysis plant is a uniquely designed tire recycling equipment that adopts the pyrolysis technology when it comes to recycling waste tires into fuel oil and carbon black.
These machines can generate fuel oil from all sorts of waste plastics – and the good part is, it is all done in an environmentally friendly way. Because of this, they are important when it comes to handling the waste plastic disposal problem.
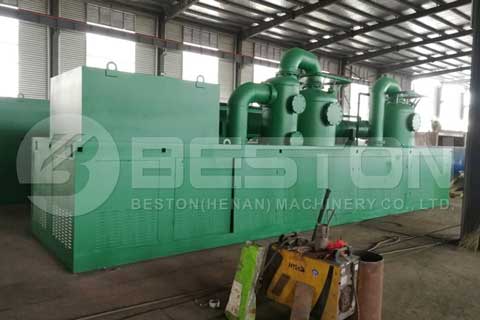
Typically, a continuous pyrolysis plant adopts a fully automatic process that may be remotely controlled through either a Programmable Logic Controller (PLC) system or a computer. Thanks to the automated/ continuous feeding and discharge system, the plant can always maintain the overall performance of a pyrolysis system nonstop.
If you are looking to learn about the working process of this continuous pyrolysis plant, along with some of the advantages it provides, read on.
The Working Process
- First, the available plastic materials are shredded into tiny plastic granules using a plastic crusher. Then, these granules are fed directly into this Beston continuous pyrolysis plant through the machine’s feeding door.
- Typically, the plant’s feeding door is constructed with an in-built screw to help you in easily conveying the earlier tiny plastic granules into the machine’s first reactor. Afterward, all the available plastic can be decomposed in very high temperatures through its first reactor, and to the second…, until all the plastic materials have gone through pyrolysis. All the carbon black powder will then be discharged into an isolated carbon black tank.
- For the oil gas produced, it will be fully cooled via water circulation. At the same time, the additional pyrolysis gas will go through recycling across the pipes into the burners where the heating process is repeated. Typically, a continuous pyrolysis plant comprises a water circulation system, along with an extra pyrolysis gas recycling system. Generally, all these help you in saving on both water and overall energy bills. In the long run, you will maximize your returns.
What Are the Advantages?
- Reduced labor cost. As aforementioned, a fully continuous plant is usually controlled by a uniquely designed PLC system and possesses automatic feeding, along with a discharge system. That means you only need one to a few employees to operate the PLC system or computer. Because of its continuous process, it may also save time and energy.
- High oil output and large capacity. Furthermore, because of having a system that enables constant feeding and discharging – and consists of multiple reactor designs – the plant can create a substantial capacity of waste tires daily. Because it offers complete pyrolysis of waste tires, the machine can produce high oil output.
- Allows internal rotating for effective continuous operation. With the external rotating system, you literally need to keep changing the plant’s seal material after every several days. The good news is that a continuous pyrolysis machine adopts the internal rotating method. Because of this, you don’t have to be concerned about changing the sealing.
- Prolonged working life. With this continuous waste tyre pyrolysis plant, indirect hot air heating is needed for heating the reactors. For this reason, the reactor will not be much damaged, thus a long usage life.